Breaking Barriers
A Safer Future for Industry
Industries dealing with hazardous materials—such as chemicals, biohazards, pharmaceuticals, and fragile electronics—face significant challenges in ensuring worker safety, reducing contamination risks, and maintaining operational efficiency. Conventional robotic systems, while effective in some applications, often lack the adaptability and gentle touch required for handling sensitive or hazardous materials. This has created a growing demand for flexible, adaptive, and damage-free automation solutions.
Soft robotics is emerging as a transformative solution for hazardous material handling. A robotic system that integrates a soft robotic arm and an adaptive soft gripper offers unparalleled benefits in safely managing delicate and dangerous substances. These innovations reduce human exposure to hazardous environments, prevent material contamination, and enhance operational efficiency across various industries.
This article explores the challenges of hazardous material handling, the role of soft robotics in mitigating risks, and the future of automation in safety-critical industries.
The Growing Need for Advanced Handling Solutions
Hazardous materials pose risks that traditional automation struggles to manage effectively. As industries seek solutions that prioritize safety, efficiency, and adaptability, the demand for soft robotic handling systems continues to rise. Unlike rigid robotic solutions, which may exert excessive force or lack flexibility, soft robotics provides an adaptable and safe alternative for delicate materials.
Soft robotic systems can be particularly useful in:
Pharmaceuticals: Ensuring precise handling of sensitive compounds and materials without contamination.
Chemical Processing: Managing reactive substances with minimal human exposure.
Biotech & Cleanrooms: Reducing contamination risks while maintaining sterility.
Food and Beverage Industries: Handling fragile packaging and organic materials with care.
Nuclear and Hazardous Waste Management: Ensuring safe containment and disposal of toxic materials without risk to human operators.
Semiconductor Manufacturing: Delicately handling sensitive microchips and wafers without introducing defects.
Soft robotic systems can be particularly useful in:
Pharmaceuticals: Ensuring precise handling of sensitive compounds and materials without contamination.
Chemical Processing: Managing reactive substances with minimal human exposure.
Biotech & Cleanrooms: Reducing contamination risks while maintaining sterility.
Food and Beverage Industries: Handling fragile packaging and organic materials with care.
Nuclear and Hazardous Waste Management: Ensuring safe containment and disposal of toxic materials without risk to human operators.
Semiconductor Manufacturing: Delicately handling sensitive microchips and wafers without introducing defects.
The continuous growth of these industries demands innovative solutions that can meet both safety standards and efficiency expectations.
Challenges in Hazardous Material Handling
Industries that work with hazardous materials must navigate multiple challenges:
1️⃣ Worker Safety Risks: Exposure to toxic chemicals, high temperatures, and biohazards can lead to severe health consequences for human workers. Reducing direct human contact with hazardous substances is critical for ensuring long-term workforce health and safety.
2️⃣ Material Sensitivity: Some hazardous materials—such as fragile pharmaceutical compounds, volatile chemicals, and biological samples—require precise and damage-free handling to prevent degradation or contamination. Mishandling of these materials can lead to inefficiencies, costly waste, and even dangerous chemical reactions.
3️⃣ Contamination Prevention: In industries like pharmaceuticals, biotechnology, and semiconductor manufacturing, even minor contamination can lead to expensive recalls, compromised product quality, and regulatory non-compliance. The demand for sterile and contamination-free operations has led to the search for better, automated solutions.
4️⃣ Rigid Automation Limitations: Traditional robotic systems lack the dexterity needed to handle soft, delicate, or irregularly shaped materials without damage. Hard robotic arms and grippers can apply excessive force, leading to breakage, spills, and inefficiencies in hazardous material handling.
5️⃣ Regulatory Compliance: Industries handling hazardous materials must comply with strict safety regulations like OSHA, FDA, and GMP guidelines. Meeting these regulations requires high-precision, controlled material management systems that can function reliably in hazardous environments.
6️⃣ High Operational Costs: The cost of manual handling of hazardous materials is not only high due to labor expenses but also due to safety protocols, compliance measures, and risk mitigation strategies. The need for cost-efficient and scalable automation is growing rapidly.
7️⃣ Complexity in Secure Transportation: Certain hazardous materials require specialized handling during transportation to prevent leaks, spills, or exposure to contaminants.
8️⃣ Lack of Adaptability in Existing Systems: Many industries still rely on rigid, outdated automation systems that struggle to meet the modern demands of hazardous material handling.
These factors highlight the need for a new generation of robotic solutions that can navigate complex environments while ensuring maximum safety and precision.
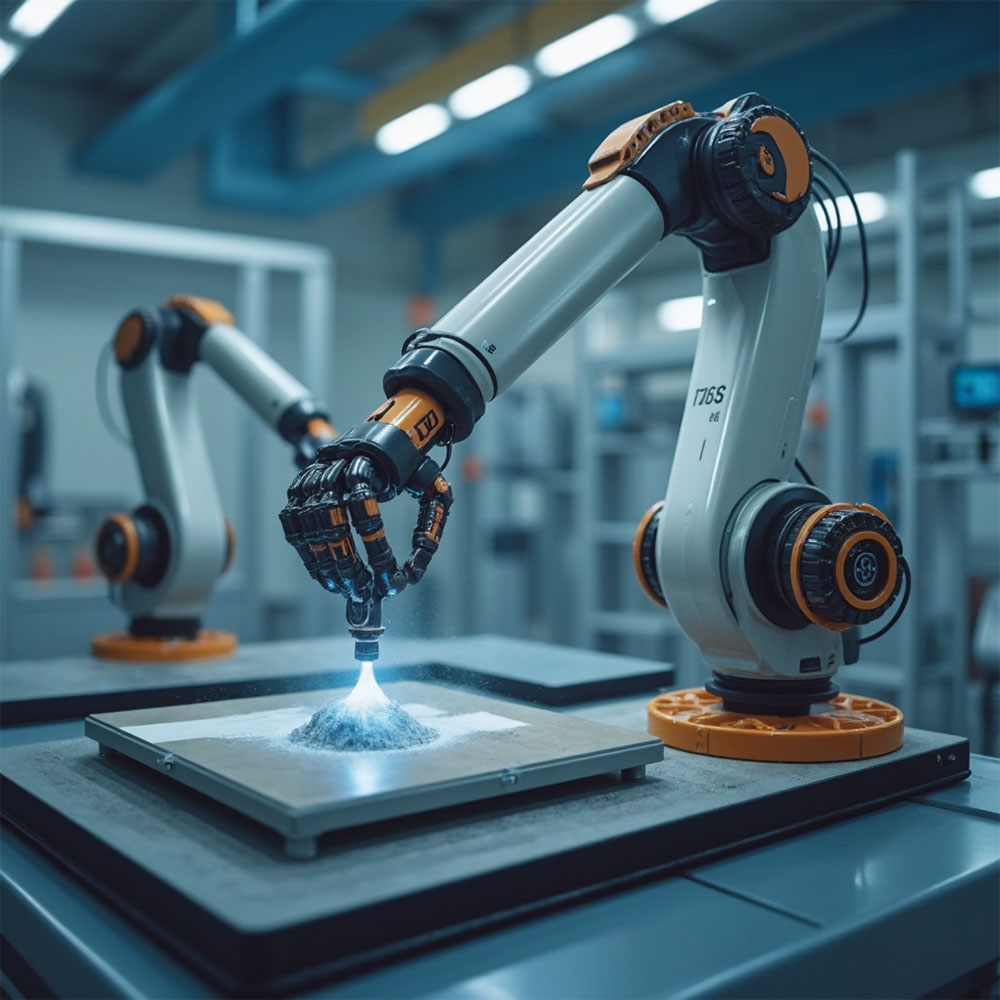
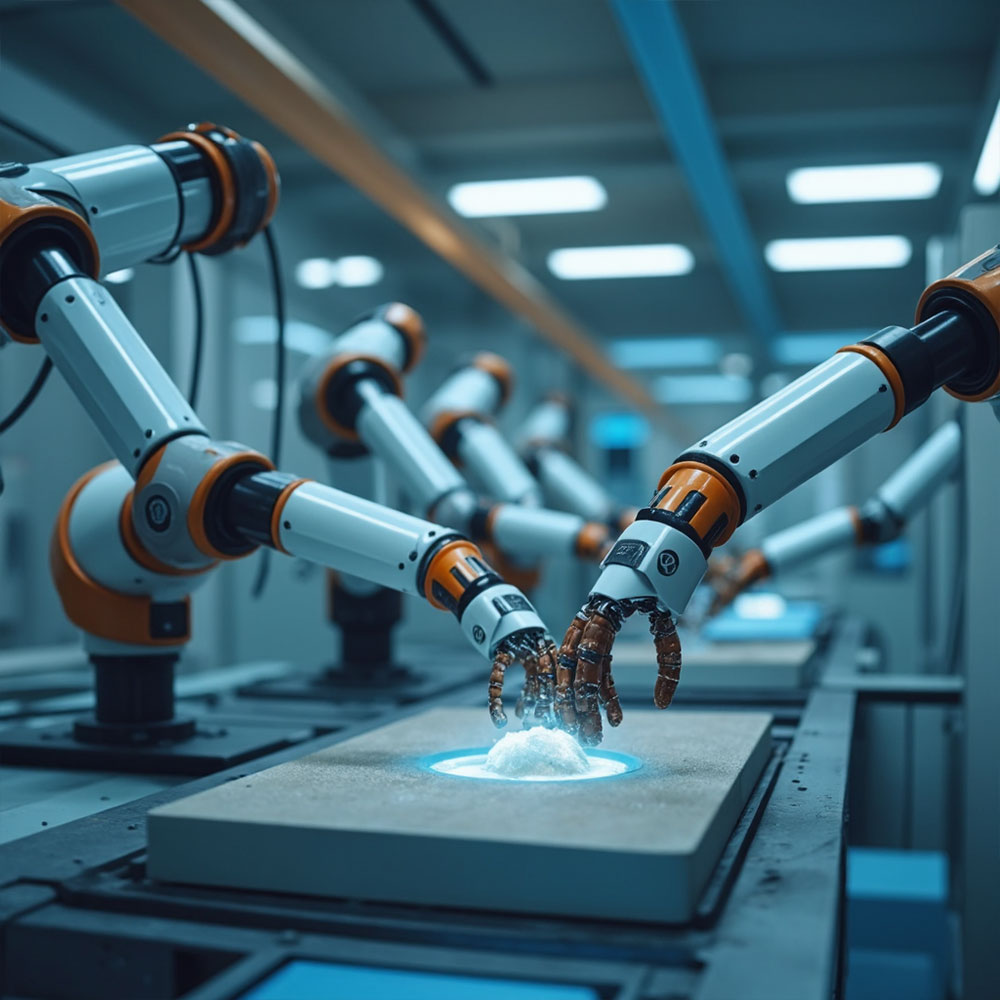
How Soft Robotics is Transforming Hazardous Material Handling
Soft robotics is designed to address these challenges by providing gentle, adaptable, and contamination-free handling solutions. The integration of a soft robotic arm and an advanced soft gripper system offers key benefits for industries dealing with hazardous materials:
Enhancing Workplace Safety
✅ Reducing Human Exposure: Soft robotic systems handle hazardous substances remotely, eliminating direct contact with toxic or biohazardous materials.
✅ Lower Risk of Workplace Accidents: Automating hazardous material handling significantly decreases workplace injuries, chemical burns, and exposure risks.
✅ Smoother Operations in High-Risk Environments: Soft robotic systems improve efficiency in environments where temperature extremes, toxicity, or radiation pose significant challenges.
✅ Minimizing Chemical Exposure Risks: By reducing human interaction with harmful substances, soft robotics minimizes risks associated with long-term exposure to toxic environments.
Safe Handling of Fragile and Volatile Materials
✅ Minimizing Product Damage: Soft robotic grippers adapt to material shape, ensuring that fragile chemicals, delicate biological samples, or reactive compounds remain intact.
✅ Customized Control & Precision: Unlike rigid robots, soft robotic systems can adjust grip force dynamically, allowing for careful handling of different materials without damage.
✅ Reducing Waste: Damage-free handling leads to lower waste and better material utilization in high-value industries like pharmaceuticals and biotech.
✅ Ensuring Consistency in Hazardous Environments: Automated control reduces human variability, ensuring a consistent, repeatable material-handling process.
Improving Contamination Control & Compliance
✅ Sterile, Contact-Free Operations: Soft robotic systems operate within cleanrooms and sterile environments, reducing the risk of contamination.
✅ Compliant with Industry Regulations: Automated handling ensures that strict regulatory requirements (OSHA, FDA, GMP, etc.) are met consistently.
✅ Non-Damaging Sorting & Packaging: Soft robotic grippers can sort and package hazardous materials without introducing contaminants, preserving product integrity.
✅ Reducing Cross-Contamination Risks: By eliminating direct human contact, soft robotics enhances sanitation protocols in sensitive industrial environments.
Increasing Efficiency & Scalability in Hazardous Environments